Wie funktioniert vorausschauende Instandhaltung mit KI?
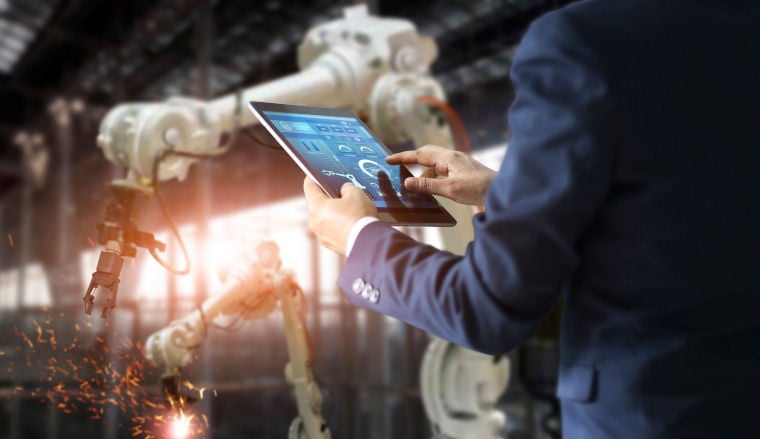
Künstliche Intelligenz (KI) scheint noch immer Science-Fiction, mit sprechenden Maschinen und fühlenden Robotern, zu sein – Bücher und Filme prägen dieses Bild seit Jahren. Aber KI ist längst in der Gegenwart angekommen, mit praktischen Anwendungsgebieten.
Dort, wo große Datenmengen und komplexe Zusammenhänge aufeinandertreffen, helfen computergestützte Tools und Lösungen bei der deren Auswertung und Organisation. Im industriellen Umfeld sind dies typischerweise digitale Produktionsleitsysteme, offiziell Manufacturing Execution System (MES) genannt. Solche Systeme sorgen für die Datenerfassung und -auswertung, sodass ein digitales Abbild der Produktion entsteht. Das wiederum ermöglicht eine effektive Kontrolle, Steuerung und Analyse ganzheitlicher Fertigungsprozesse und eröffnet Optimierungspotentiale. Grundlage sind große Datenmengen, die an Maschinen und Arbeitsplätzen, in Lager- und Transportvorgängen und bei vielem mehr erhoben werden. MES-Lösungen arbeiten sehr effektiv und helfen Unternehmen dabei, Prozesse nachhaltig zu verbessern – Künstliche Intelligenz bietet hier zusätzliches, extrem hohes Steigerungspotential, da sie vorausschauende und autonome Steuerungsvorgänge möglich macht.
Das nachfolgende Interview ist im März 2021 im Rahmen der Zusammenarbeit der aiXbrain GmbH mit der GFOS mbH entstanden. Dabei wurde unser aiXbrain-Geschäftsführer Alexander Engels zu den Möglichkeiten von KI für die Instandhaltung befragt.
Vorausschauende Instandhaltung mit Hilfe von Künstlicher Intelligenz
Kommt es bei Maschinen oder Produktionsstrecken zu Störungen oder Ausfällen, so ist dies auch in den erfassten Daten sichtbar, denn Maschinen- und Messwerte weichen von Sollwerten ab und diese Daten fließen in die Datenbanken. MES-Tools analysieren die Daten, sodass mögliche Fehlerquellen identifiziert und behoben werden können. Aber wie wäre es, wenn hier schon frühzeitig und somit vor einem drohenden Produktionsausfall eine Warnung oder gar eine Korrektur möglich wäre?
Herr Dr. Engels, zunächst herzlichen Dank dafür, dass Sie sich die Zeit für dieses Interview nehmen. Bevor wir zur obenstehenden Frage kommen, lassen Sie uns einmal vorne anfangen: Können Sie einen groben zeitlichen und technologischen Abriss zum Thema Künstliche Intelligenz geben und sagen, warum KI-Lösungen gerade jetzt eine so stark steigende Verbreitung finden?
Dr. Alexander Engels: Die Ursprünge von Künstlicher Intelligenz reichen sehr weit zurück. Ideen zu künstlichen neuronalen Netzen etwa kamen bereits Mitte des letzten Jahrhunderts auf. Deren praktische Umsetzung und sinnvolle Anwendung war aber von Beginn an eng mit der Verfügbarkeit von Daten und Rechenleistung verbunden. Es verwundert daher nicht, dass der Einsatz neuronaler Netze, etwa zur Sprachverarbeitung, selbst um die Jahrtausendwende noch eher belächelt wurde. Nur wenige Jahre später jedoch haben die Massennutzung des Internets, Rechenleistung in Cloud und auf Grafikkarten sowie die Entwicklung einiger schlauer Verfahren zum Trainieren neuronaler Netze zu einem regelrechten Durchbruch in der automatisierten Sprach- und Bildverarbeitung geführt. Weitere Modelle und Verfahren des maschinellen Lernens sind seitdem weiterentwickelt worden und der Anwendungsfokus hat sich auf fast alle Arbeits- und Lebensbereiche ausgedehnt. Nun haben wir begonnen, alles miteinander zu vernetzen und auch Maschinendaten für KI verfügbar zu machen. Der Startschuss liegt hier noch nicht allzu weit zurück, ein oder zwei Jahre vielleicht. Die Geschwindigkeit im Rennen um den wertschöpfenden Einsatz von KI im Produktionsalltag aber wird bald alles bisher Dagewesene in den Schatten stellen.
Gibt es unterschiedliche Formen der Künstlichen Intelligenz und lässt sich dies an Anwendungsszenarien veranschaulichen?
Dr. Alexander Engels: Da Künstliche Intelligenz im Grunde genommen eine Verbundtechnologie aus Mathematik, Informatik, Rechenhardware und teilweise auch noch Anwendungsfeld ist, gibt es eine ganze Reihe verschiedenartiger Definitionen, von technisch bis philosophisch. Ich persönlich würde KI nach ihrer Zweckmäßigkeit unterscheiden, und zwar in 3 Grunddisziplinen: Erstens Mustererkennung, etwa zum Aufdecken von Unregelmäßigkeiten oder zur Diagnose bei Störungen. Zweitens Prognose, etwa zur frühzeitigen Erkennung sich anbahnender Materialfehler oder von Problemen im Prozessablauf. Und Drittens Steuerung, also die Unterbreitung konkreter Handlungsvorschläge durch eine KI, etwa zur Parametrierung von Planungsvorgängen oder zum Ansteuern von Maschinen. Ein typischer und durchaus sinnvoller KI-Pfad für Unternehmen entlang dieser Grunddisziplinen würde vermutlich „Erkennen, Verstehen, Vorhersagen, Gegensteuern“ lauten.
Vereinfacht gesagt nutzen KI-Systeme Daten, um Muster und Regelmäßigkeiten zu finden und daraus zu lernen. Besteht bereits eine Datengrundlage, wie es ja beispielsweise bei laufenden MES-Lösungen der Fall ist, kann das KI-Tool sehr effektiv lernen. Aber wie muss man sich dieses Lernen als Laie vorstellen?
Dr. Alexander Engels: Im Grunde nicht viel anders als das klassische menschliche Lernen im Alltag oder bei einer Ausbildung. Der KI-Lehrling geht sozusagen in die KI-Schule. Nur dass der KI-Lehrling um ein Vielfaches schneller lernen kann, sofern er denn genügend Anschauungsmaterial in ausreichender Qualität vorfindet. Wie sein menschliches Pendant lernt auch der KI-Lehrling von den Dingen, die er beobachtet, bzw. den Daten und Informationen, die er während seiner Ausbildung zugeführt bekommt. Oder auf gut Deutsch gesagt: Was der Lehrling noch nie in irgendeiner Form gesehen hat, kennt er auch nicht. Mit jedem neuen Datensatz kalibriert der KI-Lehrling seine internen Stellschrauben, also die Parameter des unterliegenden KI-Modells. Wenn sich die Stellschrauben nur noch wenig ändern, ist die Lehre abgeschlossen. Ein Nachjustieren erfolgt dann nur noch, wenn neue Dinge passieren, das allerdings bereits im Arbeitsalltag. Gedankliche Transferleistungen, die ein Mensch ab einem gewissen Wissensstand vollziehen kann, gehen dem KI-Lehrling allerdings ab. Er ist daher ausschließlich auf einen klar abgegrenzten Aufgabenbereich fokussiert. Ohne es hier näher ausführen zu wollen, sei jedoch gesagt, dass es den besonders spannenden KI-Forschungsbereich des Transfer Learnings gibt.
Künstliche Intelligenz ist generell in jedem Bereich einsetzbar, der datenbasiert arbeitet. Worin liegt für Sie der spezielle Reiz an der Anwendung im Kontext der Fertigungsindustrie?
Dr. Alexander Engels: Die Fertigungsindustrie ist mit ihren hochkomplexen Mensch-Maschine-Systemen und mit teils bis auf die Sekunde getakteten Prozessen unglaublich vielfältig und herausfordernd. Jede Fabrik hat ihr Eigenleben, keine Werkhalle gleicht in Ausstattung und Abläufen der anderen. Dennoch haben kluge Menschen und gewiefte Ingenieure es über Jahre und Jahrzehnte hinweg geschafft, auch komplexeste Fabriken leistungsfähig aufzustellen und effizient zu betreiben. Der Preis dafür ist allerdings häufig eine gewisse Starrheit im Betriebsablauf, bei dem alles exakt aufeinander abgestimmt ist. So wie beim berühmten Schweizer Uhrwerk. Wenn aber nun Dinge wie etwa Maschinenverfügbarkeit, Materialzufuhr oder Taktzeiten im Tagesbetrieb zu weit vom Soll-Wert abweichen, funktionieren die geplanten Abläufe nicht mehr und es kommt zu teils massiven Quereffekten auf das gesamte Uhrwerk. Und wenn der Mensch in solchen Situationen nicht in der Lage ist, diese Quereffekte umgehend auszuregeln, wird Geld verloren. Die Fertigungsindustrie zeichnet sich also aus durch ihre sehr hohe Komplexität, viele Daten und große Wertschöpfungspotenziale. Das ist die perfekte Spielwiese für Künstliche Intelligenz und darum spielen wir hier mit.
Zu Beginn stand das Beispiel, dass eine KI-basierte Instandhaltung drohende Störungen oder Ausfälle frühzeitig erkennt. So können rechtzeitig Wartungs- und Instandhaltungsmaßnahmen durchgeführt werden – der reibungslose Ablauf der Produktion ist gewährleistet. Können Sie dieses Szenario ein wenig genauer beschreiben und erklären?
Dr. Alexander Engels: Das Ausgangsszenario in der Fabrik habe ich ja bereits im vorherigen Punkt beschrieben, also das perfekt geplante Schweizer Uhrwerk. Stellen wir uns nun vor, dass sich das Uhrwerk in mehrere aufeinanderfolgende Fertigungsstufen gliedert. Diese Stufen müssen ineinandergreifen, eine nach der anderen, damit aus dem Rohmaterial am Fabrikeingang das Endprodukt am Fabrikausgang wird. Und an eben diesem Ausgang wartet bereits der Kunde und drängelt, da er ja bekanntlich gestern bereits seine Lieferung bekommen sollte. In genau dieser Situation fällt nun unerwartet eine Maschine im vorletzten Fertigungsschritt aus. Und natürlich ist es genau die Maschine, auf der das Produkt läuft, auf das der Kunde wartet. Und selbstverständlich passiert das Ganze in der Nachtschicht, in der weder die Planungsabteilung da ist, noch das Personal, um zügig eine alternative Maschine umzurüsten. Wäre es nicht wunderbar, wenn es ein „Orakel“ gäbe, dass bereits in der Frühschicht auf ein mögliches Problem in der Nachtschicht hingewiesen hätte und vielleicht auch noch direkt eine Diagnose mitliefert hätte, was genau voraussichtlich schief gehen wird? Genau diese Fähigkeiten besitzt eine gut antrainierte Instandhaltungs-KI, die dann komfortabler Weise auch noch als digitaler Assistent im MES arbeitet.
Welche Bedeutung hat das Werkzeugmanagement für einen reibungslosen Produktionsablauf aus Ihrer Sicht? Ist hierbei das Wissen um Verschleiß und drohenden Ausfall besonders wertvoll?
Dr. Alexander Engels: Gerade bei Fertigungsprozessen wie der Kaltumformung oder dem Trennen heißt es für Werkzeuge in der Regel „Stahl auf Stahl“. Damit ist klar, dass die Standzeit solcher Werkzeuge begrenzt ist. Die Frage ist also immer, wie lange oder wie viele Werkstücke hält das Werkzeug noch durch, ehe es gewechselt werden muss? Bei lange laufenden Prozessen oder großen Losen ist es für die Produktionsplaner immer mit einem gewissen Risiko verbunden, kommende Schichten mit bereits lange laufenden Werkzeugen zu planen. Andererseits sind Werkzeuge oder Werkzeugteile häufig ein knappes Gut, da sie Geld kosten und Kapital binden. Das Tückische am Werkzeugverschleiß ist, dass er effektiv von einer ganzen Reihe von Faktoren abhängig ist, bspw. Rohmaterial, Hub, Kraftauslegung, Anzahl Anfahrvorgängen, usw. Bloße Statistik wie etwa Mittelwerte greifen demnach zu kurz und sind unzuverlässig. Mit eine KI-Prognose auf den effektiven Werkzeugverschleiß, die alle verfügbaren Randinformationen berücksichtigt, lässt sich hier Licht ins Dunkel bringen. Es sind vielleicht nicht unbedingt die besten Neuigkeiten, wenn die Planer:in am Morgen erfährt, dass wichtige Werkzeuge für den kommenden Tag nicht durchgängig zur Verfügung stehen werden. Das ist aber allemal besser als das Ausfallszenario in der Nachtschicht und das Chaos am nächsten Morgen.
Die Instandhaltung sowie der große Bereich der Werkzeugverwaltung sind ein Bereich, der generell viel Optimierungspotential bietet, da Störungen und Ressourcenknappheiten stets Produktionsausfälle und damit Geldverlust bedeuten. Welche anderen Bereiche und Prozesse innerhalb der Produktion sehen Sie als äußerst KI-geeignet an?
Dr. Alexander Engels: Grundsätzlich bietet KI die ganz große Gelegenheit, all die kleinen und großen Probleme im Betriebsablauf, die jeder Fertigungsbetrieb kennt, und denen bisher nur mit hohem Ressourcenaufwand beizukommen ist, mit einem völlig neuen Werkzeugkasten zu beheben. Voraussetzung hierfür ist eine ausreichende Datenlage und der Wille des Anwenders, sich auf die neuen und teils vielleicht auch etwas unintuitiv wirkenden KI-Assistenten einzulassen. Wenn beides erfüllt ist, reden wir etwa über den Einsatz von KI zur Qualitätssicherung, und zwar direkt im Fertigungsprozess an der Maschine und in möglichst frühen Wertschöpfungsstufen. Dann reden wir über die Perfektionierung der Materialflussplanung, also die Sicherstellung der kosteneffizienten Verfügbarkeit von Rohmaterialien, Halbzeugen und Personal. Oder auch Dingen wie der Erkennung und dem Aussteuern von Engpässen im Materialeinkauf oder der Lagervorhaltung, lange bevor sie tatsächlich auftreten. Da kann man leicht in’s Schwärmen kommen und sich vielleicht auch in Gedanken verlieren, die zu weit entfernt sind vom Status quo. Wichtig ist, hemdsärmelig an einer sinnvollen Stelle zu beginnen, mit den gewonnenen Erfahrungen einen KI-Fahrplan zu entwerfen und weiterzuentwickeln, die Mitarbeiter im Prozess mitzunehmen, und natürlich, sich kompetente und verlässliche KI-Partner mit ins Boot zu holen.
Herr Dr. Engels, vielen Dank für das Gespräch – wir sind uns sicher, dass weitere spannende Interviews folgen werden, um die Künstliche Intelligenz und ihre Möglichkeiten für die Industrie noch genauer zu beleuchten.
Eine leistungsstarke Kooperation für Ihren Erfolg
Die aiXbrain GmbH ist mit der GFOS mbH eine enge Zusammenarbeit eingegangen, um die bewährten IT-Lösungen im Bereich Manufacturing Execution Systems mit professionellen KI-Modulen zu ergänzen. Ausschlaggebend für die Kooperation war die hohe fachliche Kompetenz sowie der ausgesprochene Innovationswille auf beiden Seiten – so können Fertigungsunternehmen dauerhaft von leistungsstarken Softwarelösungen profitieren und die Produktionsprozesse nachhaltig optimieren.
Mehr zum Thema KI und unserer Partnerschaft mit GFOS erfahren Sie im Interview von unserem CTO Simon Görtzen und Herrn Röhrig, Beiratsvorsitzenden der GFOS.